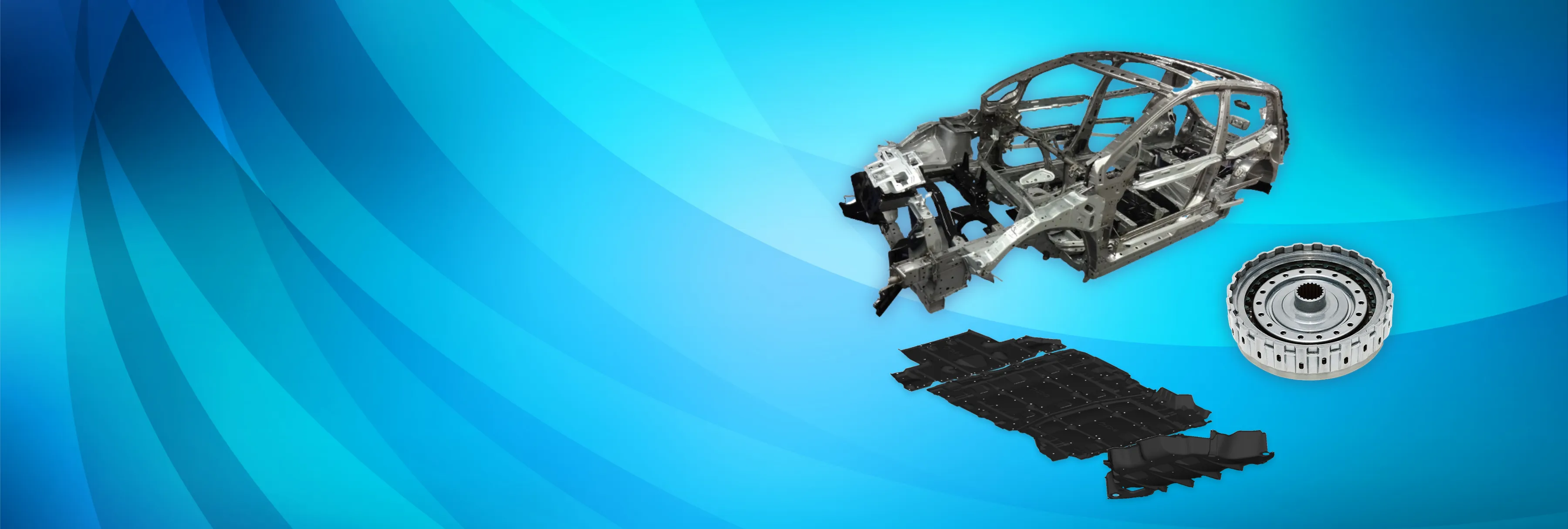
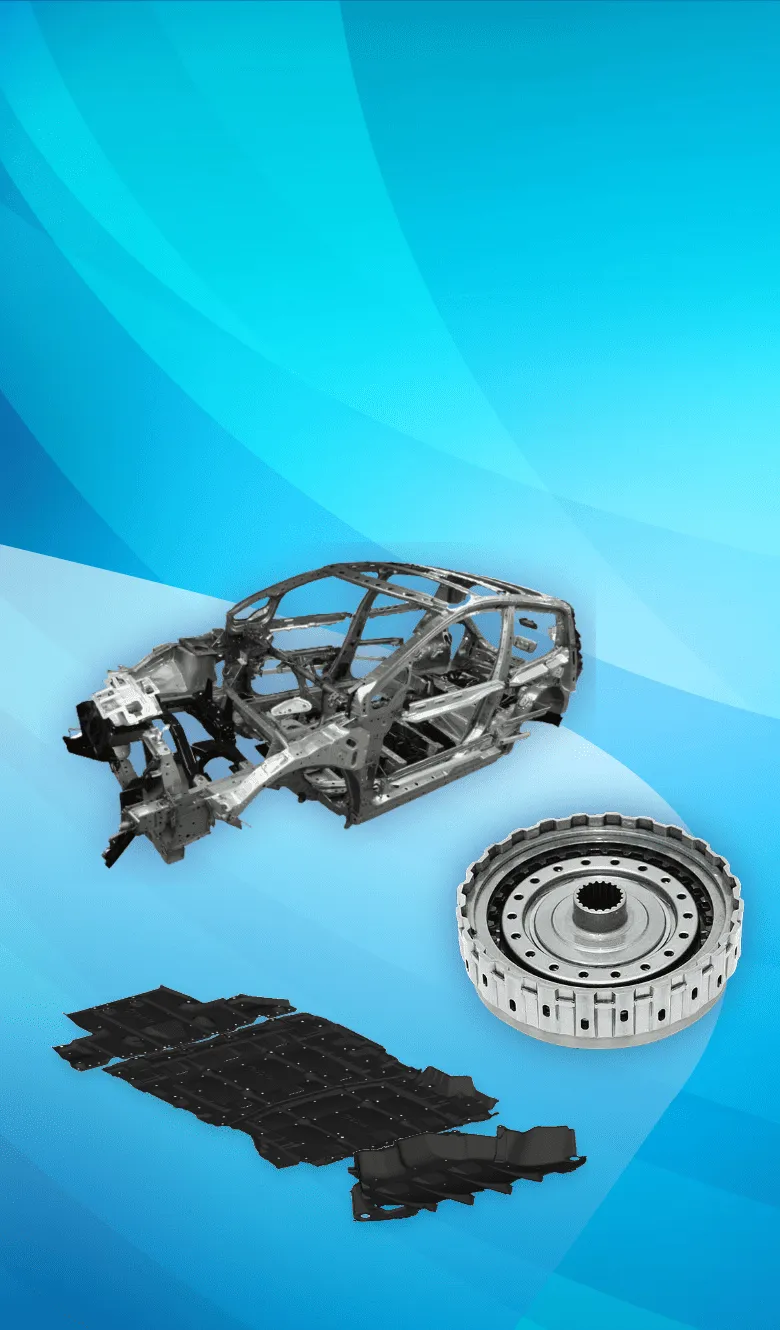
To manufacture lighter
and safer automobiles.
Unipres'
Total Press Engineering
Total Press Engineering
The manufacture of automotive parts requires three technologies: "product technology" to propose product structures and performance that meet customer demands; "production engineering" to design and develop dies and equipment necessary for parts manufacturing; and "mass production technology" to actually produce the parts.
Unipres possesses these three technologies across its Car Body Pressing, Precision Pressing, and Plastic Pressing businesses.
With automobiles requiring more advanced performance, we have continuously refined our three technologies in our three businesses through our unique "UPS activity" production system.
Reducing the weight of car body frames manufactured by Unipres significantly contributes to reducing the overall weight of the car, which in turn improves energy and fuel efficiency.
Additionally, as the body frame protects occupants during collisions, its structure is directly linked to vehicle safety performance.
All of our technologies are meant for manufacturing lighter and safer automobiles.
This is Unipres' total press engineering.
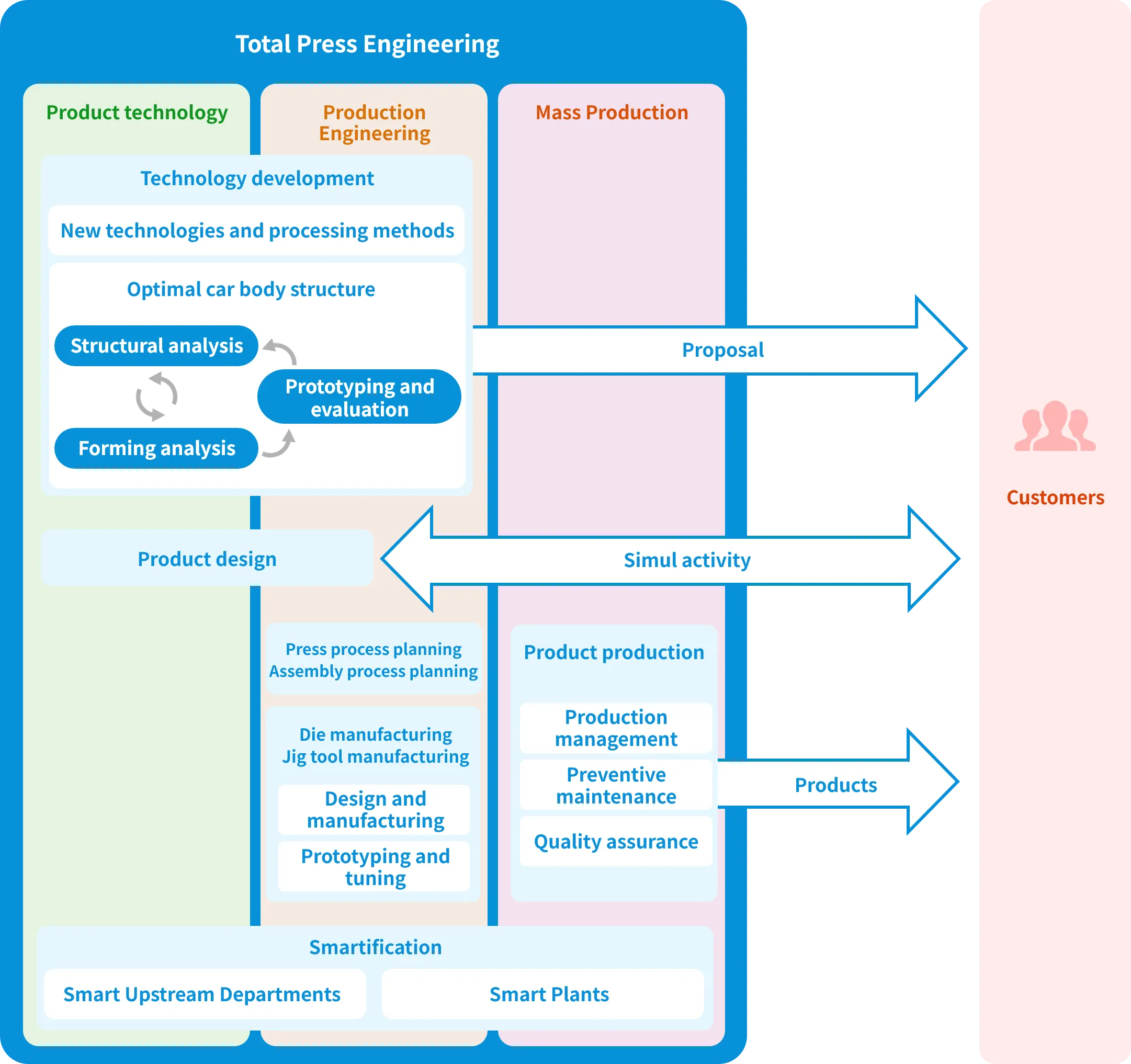
This diagram illustrates the relationship between our total press engineering and customers.
Our "product technology", which proposes product structures and performance, and our "production engineering", which designs and develops dies and equipment necessary for parts manufacturing, work together to develop new technologies and processing methods for proposing new technologies to our customers. We offer an optimal car body structure to our customers through a cycle that includes repeated structural and forming analyses as well as prototyping and evaluation.
In addition, product technology and production engineering collaborate on product design, engaging in Simul activity in which products are developed with customers from their early development stages. Production engineering involves press and assembly process planning, as well as the design, manufacturing, prototyping, and tuning of dies and jigs tools.
For mass production, we carry out production management, preventive maintenance, and quality assurance to deliver the final product to our customers. Efforts to smartify are underway in all areas. Upstream departments are implementing measures to improve productivity and reduce lead time, while plants are working on labor saving and automation to enhance existing technologies.
Product technology
-
Car Body Pressing
Car body frame parts must be both lightweight and safe. We solve this challenge by using press technology to offer an optimal lightweight car body structure, which takes into account even the assembly and joining processes.
-
Precision Pressing
Transmission parts and function parts specific to electric vehicles require not only weight reduction but also high precision and durability. Our unique press technology can offer and achieve optimal specifications.
-
Plastic Pressing
By manufacturing plastic products with a press--an innovative forming technology, we offer high-value-added press parts and contribute to the electrification of automobiles.
Production Engineering
Use of Digital Technology
We employ digital technology to create high-quality products that meet our customers' requirements. We use our proprietary forming simulations to check for forming issues from the development stage. We then conceptualize part shapes to solve these issues, propose them to our customers, incorporate them into the product, and design processing methods and die specifications accordingly. Our high quality is an outcome of considering optimal specifications from the development stage in anticipation of mass production. For assembly equipment, we conduct robot simulations prior to their actual manufacturing in order to identify production issues through data verification, and develop equipment aimed at mass production.
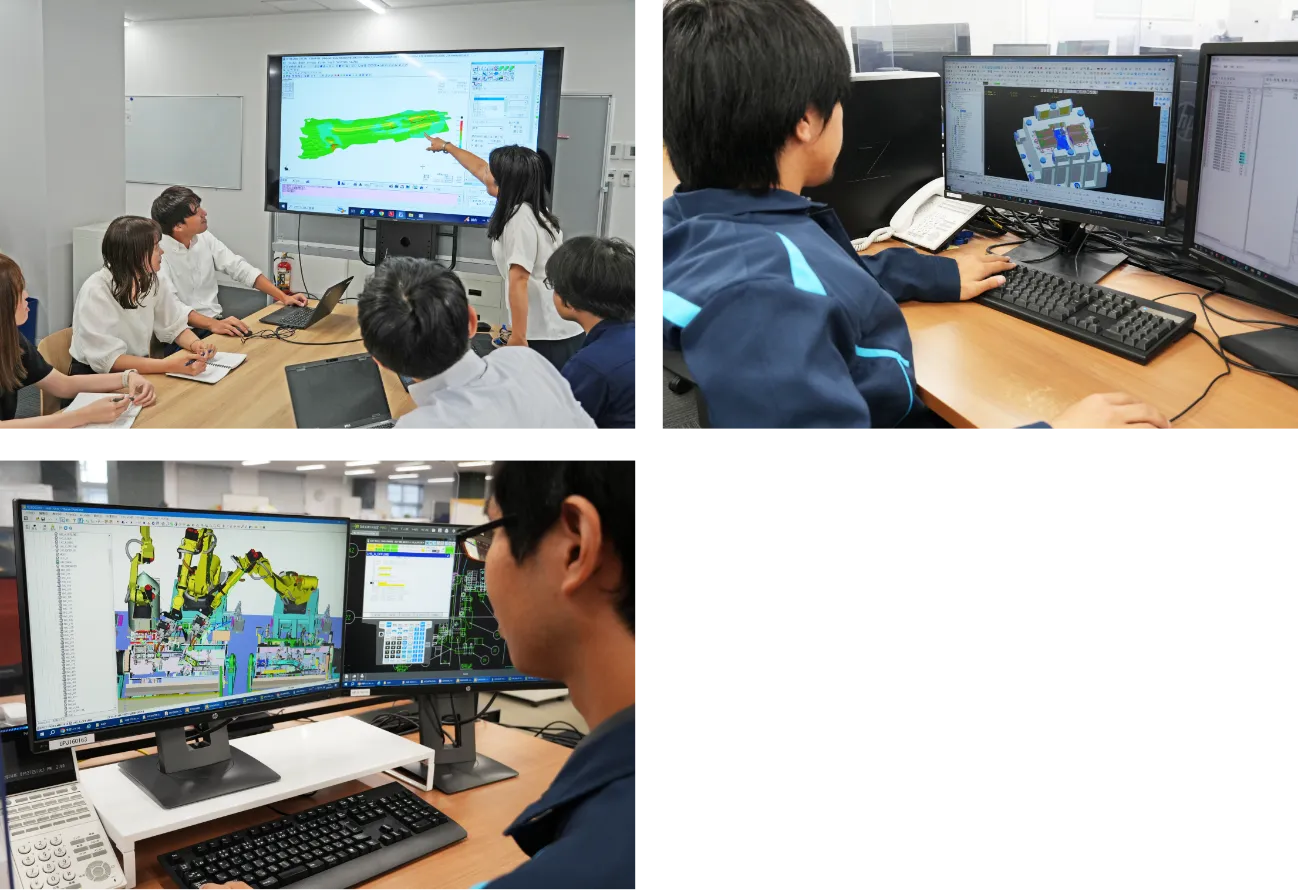
In-house Design and Manufacturing of Dies and Assembly Equipment
Unipres is capable of designing and manufacturing both dies and assembly equipment in-house. We have a wide range of machinery, from large-scale to small-scale machines, including laser processing machines, and have personnel who can expertly operate them.
Our ability to manufacture dies and assembly equipment according to our internally developed optimal specifications is none other than because we have both equipment and talent.
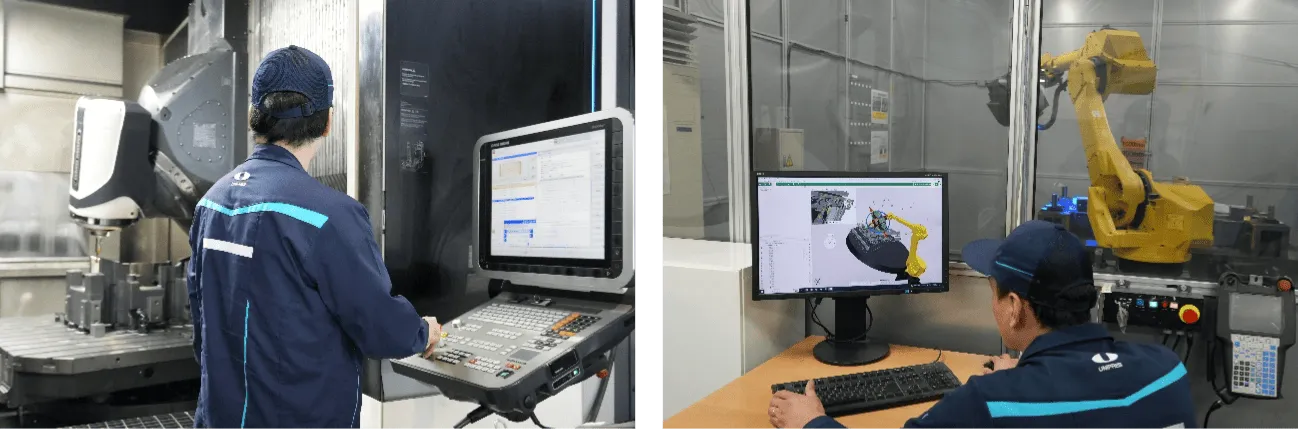
Pilot Line
We have established a pilot line in Japan with the same equipment specifications as our production plants. After conducting trials on this pilot line, we roll out the process to our production plants worldwide. By having the production plants participate in these trials, we can identify and resolve issues that may arise during mass production ahead of time and swiftly achieve mass production of high-quality products.
Mass Production
UPS Activity
The Unipres Production System (UPS) activity strives to detect all waste in work processes and reform them to make the organization more profitable and competitive.
This effort has been continuously pursued by Unipres since shortly after the merger in 1998. A parts manufacturer must efficiently make high-quality products according to customer demands and deliver them in a timely manner. To meet these demands, Unipres aims to attain higher levels of quality and efficiency in production. For this purpose, key performance indicators (KPIs) are set consistently across our plants worldwide, and plants compete with each other to achieve them. The methods to achieve KPIs for UPS activities are also standardized across all plants. The initiatives of plants that achieved their KPIs are shared as examples for other plants to follow, with the aim of triggering a spiral-up effect across the entire Group.
Functions That Support Production
More than just plants are needed to sustain mass production. All functions are essential for production according to customer demands, including quality control to maintain high product standards, production management to ensure timely deliveries, purchasing to buy materials without any excesses or shortages, human resource measures to support personnel, and accounting to manage finances. At Unipres, manufacturing is a unified effort that integrates the headquarters, upstream departments, and plants.
Smartification
Smart Plants
Unipres has always striven to reduce plant costs through UPS activities. We are currently promoting the smartification of plants to realize "plants operated with minimal personnel" and "plants that never stop."
By using technologies, such as robotics, data collection and management, sensing and monitoring, AI, and autonomous control, we are advancing labor saving and automation, increasing utilization rates, and improving good product rates and productivity.
Smart Upstream Departments
While plants are where products are produced, their entire manufacturing process begins much earlier, in upstream areas such as development, design, and fabrication. In the past, each task had an experienced "master," with much of the work relying on the master's skills. Today, however, we are advancing smartification. Efforts are being made to improve productivity and shorten lead times, including automating process planning and design through data collection/accumulation and AI, automating die designing, automating skilled or strenuous work involved in the manufacture of dies and jigs tools, and automating inspections.