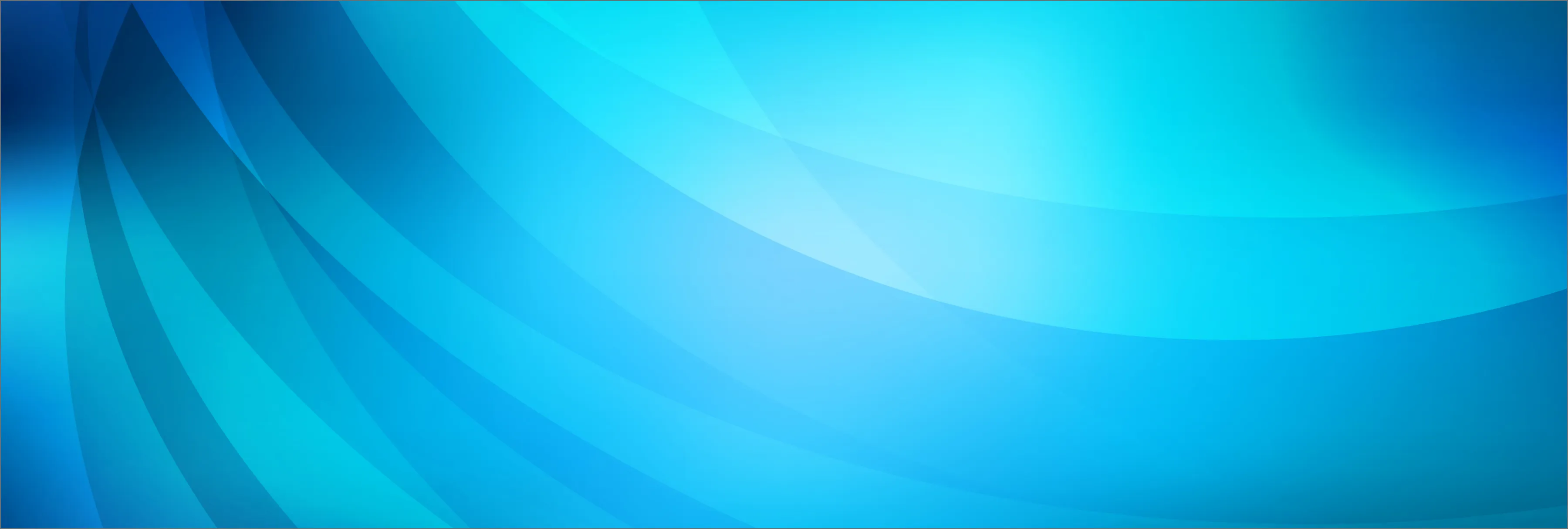
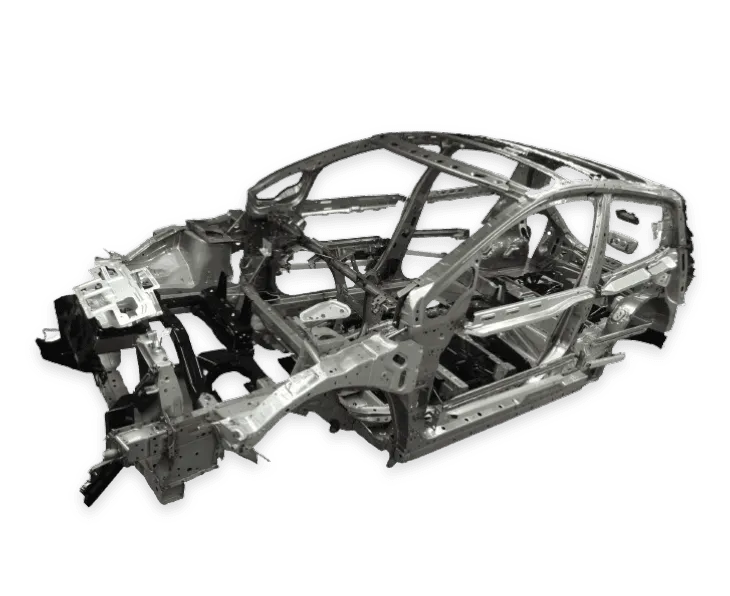
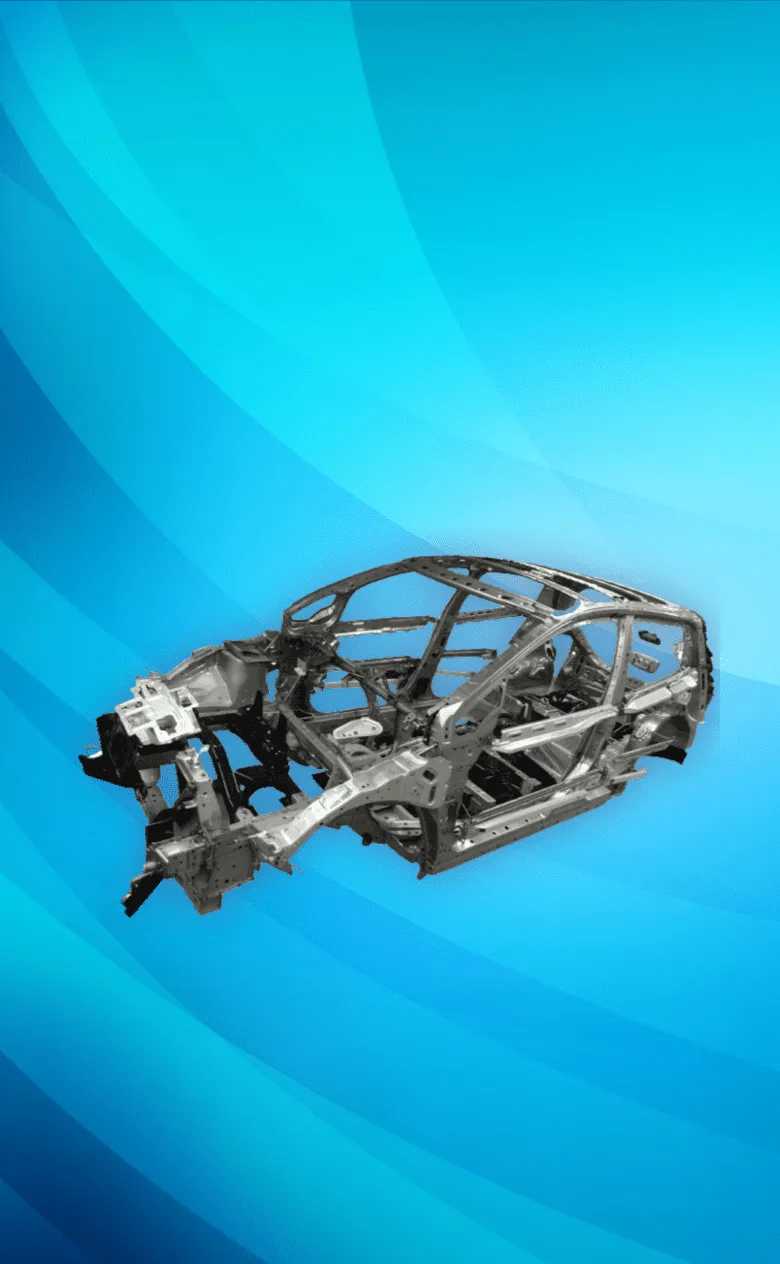
Solving the dilemma
of
lightweight versus safety
Car Body Press Products
-
Technology to Propose Car Body Structures
Staying attuned to market trends to promptly understand automakers' needs, we develop new products that offer car body structures based on our own strategy. We utilize forming analysis and collision performance analysis to propose optimal structures that are feasible for press forming, supported by car body performance evaluations. For example, through enhancing the strength of car body frame components or integrating parts, we achieve further weight reduction of car bodies and cost savings.
-
Cold Pressing Technology
We are capable of press forming a wide variety of automotive steel sheets, ranging from mild steel to ultra-high-tensile materials. For ultra-high-tensile materials that are difficult to press form, mass production is achieved by employing forming simulations to devise processing methods and design dies. We also develop and can produce aluminum press forming and production engineering.
-
Hot Stamping Technology
We use hot stamping for products that require high strength or have shapes difficult to form with cold pressing. The Company has achieved industry-leading deep drawing and contributes to the expanded application of hot-stamped components to car body frame parts. A drawback of hot stamping is slower forming speed compared to cold pressing. We have improved productivity by forming multiple parts simultaneously. Our proprietary selective hardening technology enables a single part to have different strengths, making the parts even lighter. We can also mass produce parts with different thicknesses using the patchwork, tailored welded blank, and tailored rolled blank processing methods.
-
Assembly and joining
With a view to expanding the application of aluminum parts (pressed parts, die-cast parts, and extruded parts) to car body frames, we are developing and applying new joining technologies, such as self-piercing rivets (SPR), flow drill screws (FDS), metal inert gas (MIG) welding, and adhesives, in addition to traditional spot welding. We are testing the efficient placement of these joining technologies on a part assembly pilot line, and are working to establish a mass production system capable of ensuring a stable supply of high-quality products.